Are you ready to change your THY Precision injection moulding process step by step process for the better? Industry 4.0, the fourth industrial revolution, is changing how we make plastic products. It’s about making your injection moulding process step by step better, more efficient, and innovative. Let us show you how to add these new technologies to your process step by step.
Key Takeaways
- Discover the key benefits of integrating Industry 4.0 into your injection moulding process step by step process
- Learn the step-by-step approach to revolutionize your moulding workflow with cutting-edge technologies
- Explore the latest innovations in 3D printing, additive manufacturing, and virtual reality for smarter injection moulding process step by step
- Understand how simulation and generative design can optimize your mould design and moulding cycle
- Gain insights from industry experts on the future of injection moulding process step by step in the era of Industry 4.0
The Emergence of Industry 4.0 in Plastic injection moulding process step by step
The plastic injection moulding process step by step process is changing fast thanks to Industry 4.0. This new era brings more efficiency, better productivity, and more innovation to the plastic injection moulding world.
Key Benefits of Industry 4.0
Industry 4.0 brings big changes with technologies like the industrial internet of things (IIOT), machine learning, and big data analytics. These changes help plastic injection moulding makers a lot. They get:
- More productivity and efficiency with real-time checks and predictive maintenance
- Cost savings by using resources better and cutting down on waste
- Better teamwork and communication along the whole supply chain
- More flexibility to meet market changes and customer needs
- Higher quality and better safety with strict rules and standards
- Better customer experiences with products made just for them
- More chances for new ideas and products
By using Industry 4.0, companies like THY Precision are changing the game in plastic injection moulding. They’re getting ready to win in the global market.
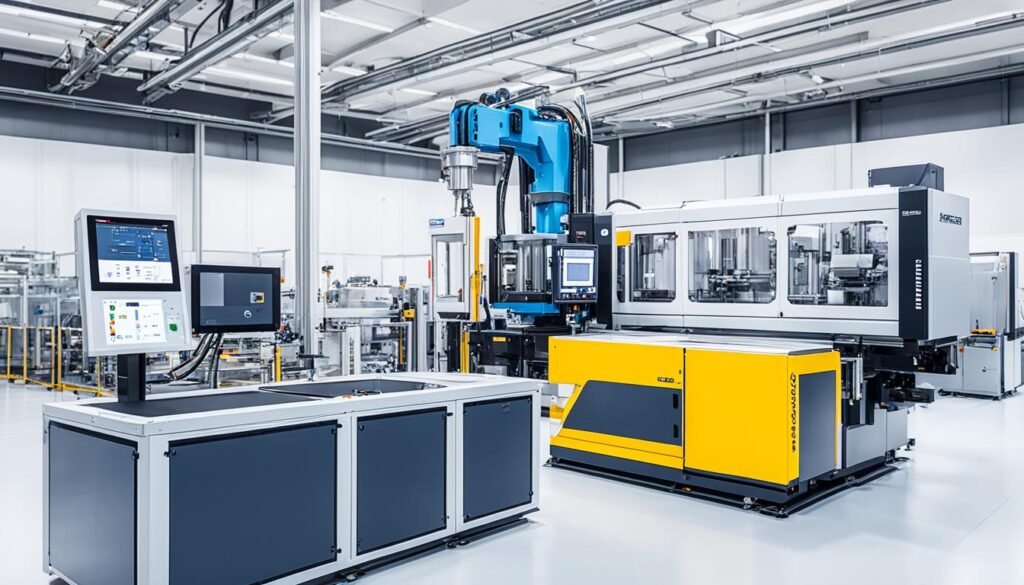
“The integration of Industry 4.0 technologies is transforming the plastic injection moulding industry, driving greater efficiency, productivity, and innovation across the entire value chain.”
The plastic injection moulding industry is always changing. Using Industry 4.0 will be key for makers who want to stay ahead. They need to keep up with their customers’ needs.
Revolutionizing the injection moulding process step by step with Industry 4.0
THY Precision is changing the game with Industry 4.0. The injectionmouldingprocessstepbystep is now faster, more efficient, and meets market needs better. This is thanks to advanced automation and connected systems in plastic injectionmoulding.
The “smart factory” is at the core of this change. THY Precision’s plants now have machines that can check data, talk to each other, and make the injectionmouldingprocessstepbystep better in real-time. This level of connection and automation lets workers focus on big-picture tasks. It’s helping the company grow in new and exciting ways.
Key Benefit | Impact on Injection Moulding Process |
---|---|
Faster Processing | Automated systems and connected equipment enable the injectionmouldingprocessstepbystep to operate at unprecedented speeds, reducing lead times and improving responsiveness to customer demands. |
Enhanced Efficiency | Intelligent monitoring and data analysis optimize every step of the injectionmouldingprocessstepbystep, minimizing waste, downtime, and errors. |
Increased Flexibility | Flexible manufacturing systems and generative design tools allow THY Precision to quickly adapt the injectionmouldingprocessstepbystep to changing market conditions and customer needs. |
THY Precision is leading the way in injectionmoulding with Industry 4.0. They’re bringing speed, efficiency, and quick response to customers like never before. This move makes them a top name in plastic injectionmoulding, ready for the future.
“The future of plastic injectionmoulding lies in the seamless integration of automation, data, and connected systems. THY Precision is at the forefront of this revolution, empowering our clients with unparalleled speed, quality, and flexibility.”
Leveraging Key Technologies for Smarter Injection Moulding
In the plastic injection moulding world, new technologies have changed the game. 3D printing is one such technology that has made a big impact. It’s a key part of additive manufacturing now.
3D Printing and Additive Manufacturing
Adding 3D printing to the plastic injection moulding process has opened up new doors. With additive manufacturing, making complex parts like metallic molds is now possible. This has cut down the time it takes to make injection molds.
Designing complex shapes and simulating the process have made the moulding process better. Thanks to 3D printing, cooling times are shorter, making the whole process faster and more efficient.
Now, making complex molds is easier with 3D printing. This has led to more innovation in injection moulding. It lets manufacturers try new things they couldn’t before.
“The integration of 3D printing into the plasticinjectionmouldingprocessstepbystep has unlocked unprecedented possibilities.”
The mix of 3D printing, additive manufacturing, and injection moulding is set to bring more changes. It will help manufacturers work better, be more flexible, and stay competitive.
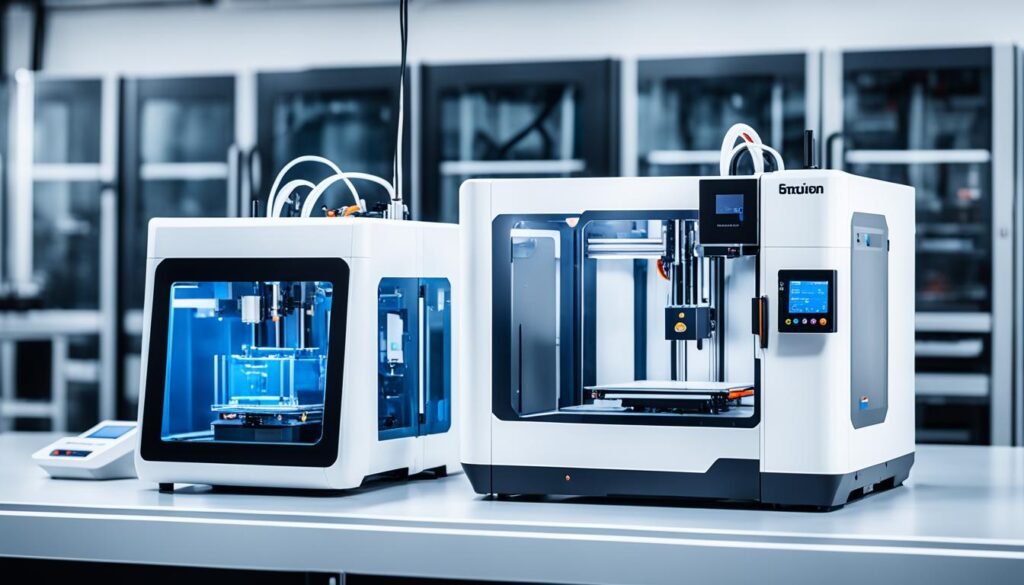
Simulation, Generative Design, and Virtual Reality
The plastic injection moulding process is changing fast. Now, we use advanced tech like simulation, generative design, and virtual reality (VR). These tools are changing how THY Precision makes products and designs them.
Simulation helps us see and check the whole process, from how materials move to how parts change shape. It lets engineers spot problems early, make better designs, and use fewer prototypes. This saves time and money and makes the process better.
Generative design is a big deal in product design. It lets THY Precision try out many different designs. By setting limits and goals, it comes up with the best solutions. This cuts down on waste and speeds up design work.
Virtual reality (VR) makes designing and developing products smoother. It connects the simulation to the people working on it. VR lets engineers and designers see how products work, spot problems, and make better choices. This tech is a big help in making products at THY Precision.
Technology | Benefits for injectionmouldingprocessstepbystep |
---|---|
Simulation |
|
Generative Design |
|
Virtual Reality |
|
By using these new technologies, THY Precision is leading the way in injection moulding. We’re making top-quality products, being more efficient, cutting waste, and staying ahead in the game.
“Simulation, generative design, and virtual reality are changing how we do plastic injection moulding at THY Precision. These tools let us innovate more and give our clients amazing results.”
Conclusion
The journey of the plastic injection moulding industry with Industry 4.0 has changed a lot. By using new tech like 3D printing and simulation, THY Precision has made their process better. This has led to more productivity, efficiency, flexibility, and new ideas.
As manufacturing changes, it’s key for companies like THY Precision to keep up with Industry 4.0. Working with experts helps them use the full potential of the process. This way, they can stay ahead and make their production better for the future.
The future of plastic injection moulding is all about using Industry 4.0 tech well. This lets companies make high-quality products, cut down on waste, and meet market demands. THY Precision is at the forefront of this change. They’re setting the bar high for the industry, aiming for a more efficient, green, and innovative future in plastic injection moulding.